An Overview of CMC in the Drug Development Process
Chemistry, Manufacturing, and Controls (CMC) is a critical component of drug development. It ensures that pharmaceutical products are consistently safe, effective, and of high quality. CMC covers the entire process of developing and manufacturing a drug, from raw material sourcing to final product formulation. It also ensures compliance with regulatory requirements, reducing the risk of delays in approval.
Without a strong CMC strategy, even a promising drug candidate can fail to reach the market. It provides the scientific and technical foundation for pharmaceutical product development, covering drug formulation, formulation development, pharmaceutical formulation development, and more.

The Role of CMC in Drug Development
CMC activities span all phases of drug development, from discovery to commercialisation. A strong CMC strategy ensures a smooth transition between these stages:
- Preclinical Formulation Development: At this stage, pharmaceutical formulation development teams work to optimise the drug’s characteristics. The goal is to create a stable, bioavailable, and scalable formulation for further testing.
- Clinical Trial Phases (I-III): As the drug progresses through clinical trials, CMC ensures that each batch meets the same standards. Any changes in formulation, production, or quality control must be documented and approved.
- Regulatory Submissions: Before a drug can be approved, regulatory agencies require detailed CMC data, including formulation in pharmaceutical industry processes and drug development CMC compliance.
Commercial Manufacturing: Once approved, pharmaceutical product development teams must ensure that large-scale production maintains the same high standards as earlier clinical batches.
Key Components of CMC
Drug Substance (Active Pharmaceutical Ingredient – API)
The API is the core of any pharmaceutical product. It is the biologically active component responsible for the drug’s intended effects.
CMC requires a full understanding of the API’s chemical properties, physical characteristics, and stability. This information is crucial for ensuring that each batch of the drug remains consistent in strength and purity. The development team must also establish robust synthetic processes to ensure efficient and scalable manufacturing.
Drug Product (Final Pharmaceutical Formulation Development)
The API alone is rarely usable as a medicine. It must be combined with excipients (inactive ingredients) to create a final dosage form, such as tablets, capsules, or injectables.
Formulation development services focus on optimising how the API interacts with excipients to enhance stability, bioavailability, and patient usability. This stage is crucial in preclinical formulation development, where early prototypes undergo rigorous testing to identify the best composition.
Manufacturing Process Development
A well-defined manufacturing process ensures that the drug can be produced consistently at scale. This includes:
- Process validation: Ensuring manufacturing methods produce identical results across multiple batches.
- Equipment qualification: Confirming that machinery operates reliably and meets regulatory standards.
- Facility compliance: Making sure the production environment meets stringent quality controls.
Formulation services must also ensure that scaling up from small lab batches to large-scale production does not impact the drug’s performance.
Analytical and Quality Control Testing
Drugs must meet strict purity, potency, and stability requirements before they can be used in clinical trials or sold commercially. This involves:
- Analytical method development: Defining tests to measure drug composition and detect impurities.
- Stability studies: Assessing how storage conditions affect the drug’s shelf life.
- In-process testing: Monitoring quality during production to catch any deviations early.
CMC pharmaceutical development requires continuous quality monitoring to maintain compliance with regulatory authorities like the MHRA, EMA, and FDA.
The Importance of CMC in Regulatory Submissions
Regulatory authorities require comprehensive CMC documentation before granting approval for clinical trials or market entry. A weak CMC strategy can lead to delays or even rejections. Key submission requirements include:
- Investigational New Drug (IND) / Clinical Trial Application (CTA): Initial submission before human testing, including drug formulation details and preclinical formulation development data.
- New Drug Application (NDA) / Marketing Authorisation Application (MAA): Full submission for commercial approval, including CMC pharmaceutical development data, stability studies, and manufacturing controls.
Post-Approval Changes: Any modifications to the drug formulation or manufacturing process must be re-evaluated and approved.
Challenges in CMC Pharmaceutical Development
CMC presents several challenges that can impact drug approval timelines:
- Scaling Up Production: A formulation that works in small lab batches may not behave the same way in large-scale manufacturing. CMC teams must develop scalable processes.
- Stability Issues: Some drug formulations degrade over time or under certain conditions. CMC teams must optimise storage and packaging solutions.
- Regulatory Variability: Different regions have different regulatory expectations. Companies must navigate complex global compliance requirements.
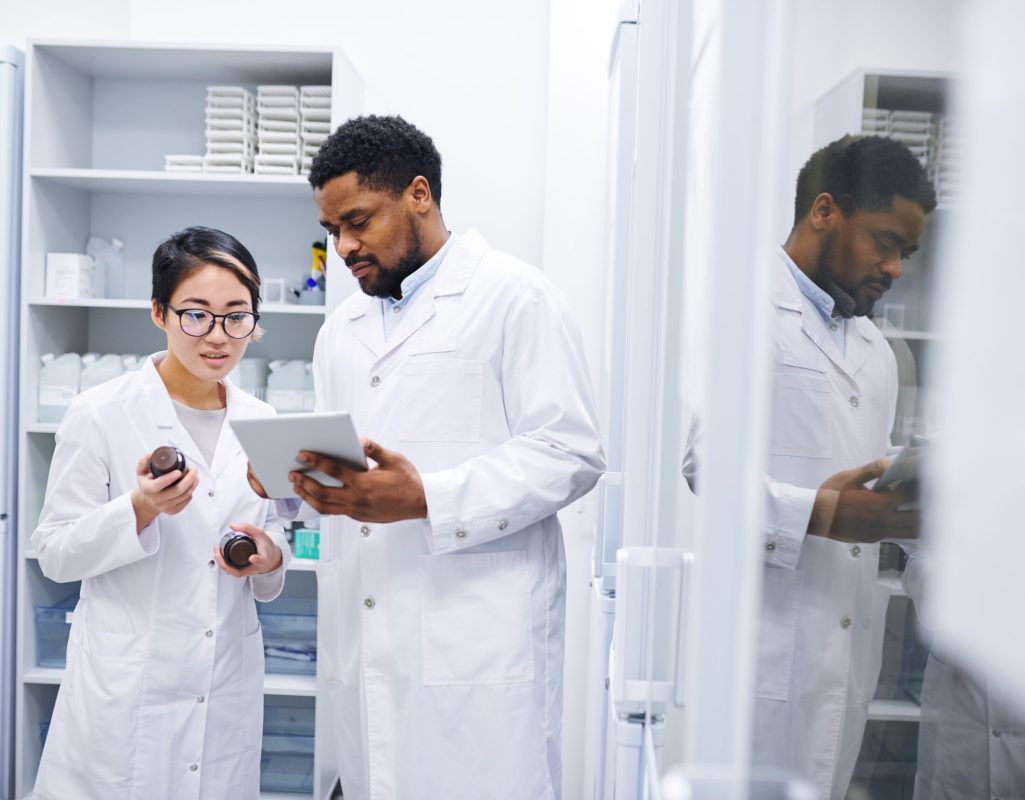
Partnering with a CDMO for CMC Drug Development
Working with a Contract Development and Manufacturing Organisation (CDMO) can streamline the CMC drug development process. Many pharmaceutical companies, particularly small and emerging biotechs, lack in-house expertise or facilities for pharmaceutical formulation development and large-scale manufacturing. CDMOs provide formulation development services, manufacturing capabilities, regulatory expertise, and quality control solutions.
Benefits of Partnering with a CDMO
1. Accelerated Formulation and Process Development
CDMOs have established expertise in preclinical formulation development, helping to identify the most effective drug formulation early. They optimise stability, bioavailability, and scalability, ensuring smooth progression through pharmaceutical development stages.
2. Cost and Time Efficiency
Developing in-house CMC pharmaceutical development capabilities requires significant investment in facilities, equipment, and personnel. CDMOs provide formulation services and manufacturing solutions without the need for these upfront costs, reducing financial risk and shortening timelines.
3. Regulatory Compliance and Risk Management
CDMOs are experienced in handling global regulatory requirements, ensuring compliance with CMC in pharmaceutical regulatory filings. They assist with drug development CMC documentation, reducing the risk of delays or rejections from regulatory agencies.
4. Scale-Up and Commercial Manufacturing
CDMOs support companies from early-stage pharmaceutical formulation development through to commercial production. They ensure smooth technology transfer, process validation, and efficient scale-up, maintaining batch consistency and quality.
Choosing the Right CDMO for CMC Pharmaceutical Development
Selecting a CDMO requires careful evaluation of their capabilities, track record, and regulatory compliance. Consider:
- Experience in your drug type (small molecules, biologics, etc.)
- Formulation development expertise in your target dosage form (oral, injectable, etc.)
- Regulatory track record and history of supporting successful approvals
- Manufacturing capacity and scalability for future commercialisation
By partnering with the right CDMO, you can reduce risk, improve efficiency, and accelerate CMC in pharmaceutical development. This allows you to focus on innovation while leveraging external expertise for drug formulation, manufacturing, and regulatory success.
Conclusion
CMC plays a crucial role in ensuring that drugs are developed, manufactured, and tested to the highest standards. It ensures consistency, quality, and regulatory compliance throughout the drug development lifecycle.
A strong CMC strategy helps pharmaceutical companies avoid regulatory delays, maintain product quality, and achieve a successful market launch. From drug formulation to large-scale pharmaceutical product development, CMC is a key factor in bringing safe and effective medicines to patients.
Frequently Asked Questions
Why is CMC important in pharmaceutical development?
CMC is essential for maintaining drug safety, efficacy, and consistency. Without robust CMC processes, drugs may not receive regulatory approval or may fail to meet quality standards.
What is formulation development in the pharmaceutical industry?
Formulation development involves optimising the combination of active and inactive ingredients to create a stable, effective, and patient-friendly drug.
How does CMC impact clinical trials?
CMC ensures that the drugs used in clinical trials meet strict quality and safety standards. Any changes in formulation or manufacturing must be thoroughly documented and approved.
When does CMC start in drug development?
CMC begins in the early stages of drug discovery and continues through preclinical formulation development, clinical trials, and commercial production.
What happens if a drug fails CMC testing?
If a drug fails CMC testing, adjustments must be made to its formulation, manufacturing process, or quality control measures before it can proceed further in development.