Enhancing API Solubility with Spray-Dried Dispersions
Spray-Dried Dispersions (SDDs) are a practical solution for improving the solubility of Active Pharmaceutical Ingredients (APIs). By leveraging spray drying, APIs are converted into amorphous solid dispersions, which enhance bioavailability. Key factors like inlet temperature and droplet size during the spray drying process help create small, uniform particles, preventing phase separation and crystallization. Using solvents such as acetone or methanol further supports the solubilization process, making SDDs a valuable tool in drug formulation.
Solubility Challenges
Many new drugs have poor aqueous solubility, which limits absorption and bioavailability. Complex molecular structures, high molecular weight, and strong intermolecular forces are common causes. Poor solubility can result in insufficient drug levels in the bloodstream, reducing therapeutic effectiveness. Addressing these solubility issues is critical for developing effective and bioavailable drugs.
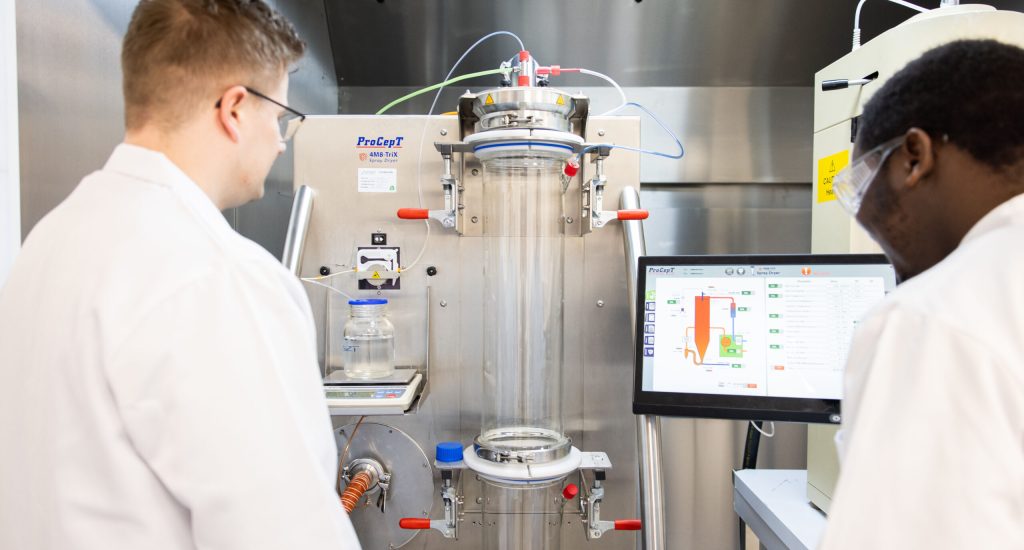
How SDDs Improve Solubility
SDDs improve solubility by dispersing the API in a polymer matrix. The spray drying process dissolves the drug and polymer in a solvent, then atomizes the mixture into fine droplets. A hot drying gas evaporates the solvent, leaving amorphous particles. This amorphous state offers better solubility and dissolution rates than crystalline forms.
Small particle sizes created during spray drying increase surface area, enhancing dissolution. The uniform mixing of API and polymer also improves solubility, ensuring faster absorption and higher bioavailability.
Spray drying creates amorphous solid dispersions that enhance solubility and bioavailability. It allows precise control over particle size and morphology, enabling tailored drug delivery. The rapid drying process also protects heat-sensitive APIs. Spray drying is scalable and efficient, making it suitable for large-scale pharmaceutical production.
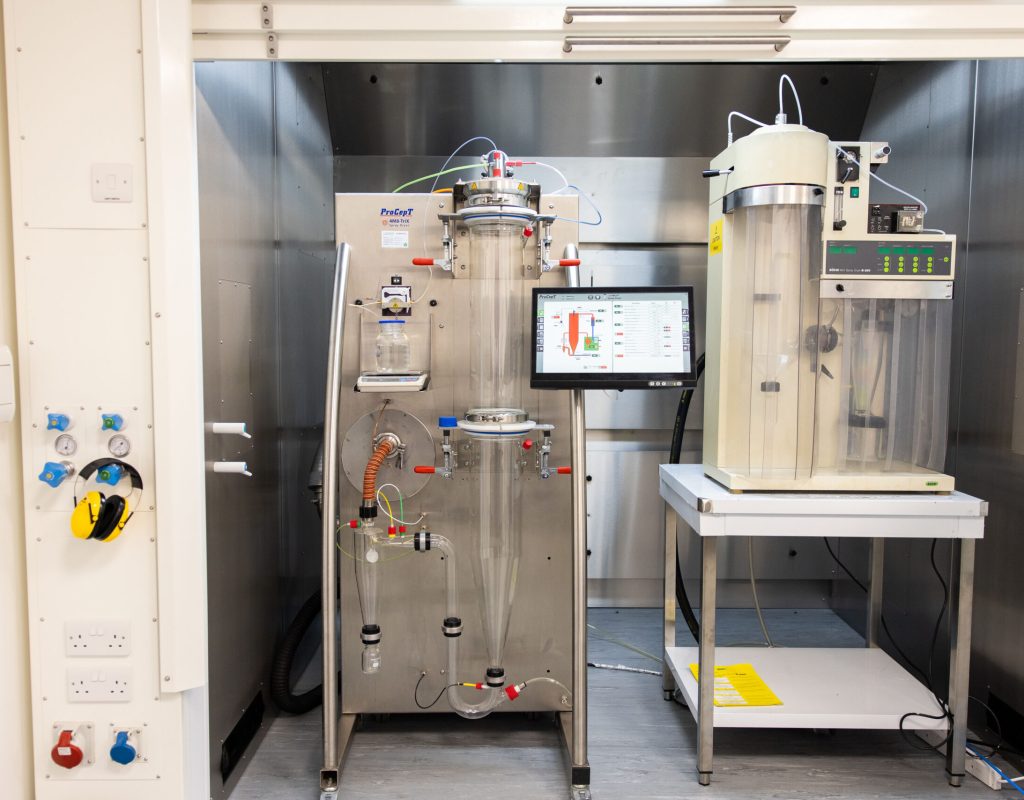
Spray Drying Technology
Spray drying transforms a liquid feed into a dry powder by atomizing it into droplets and evaporating the solvent with hot gas. This process enables the creation of uniform particles suitable for pharmaceutical applications. By controlling the inlet temperature, droplet size, and drying gas flow, you can optimize particle characteristics for solubility and stability.
BUCHI Mini Spray Dryer B-290
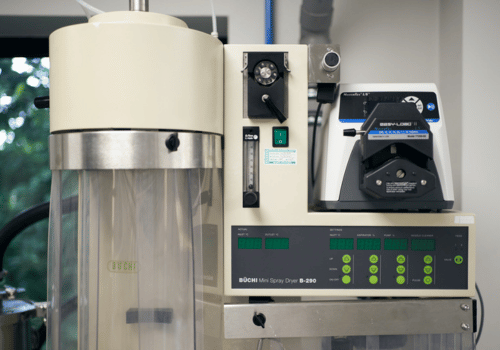
8 UNITS AVAILABLE
Typical Batch Scale
100mg – 100g
Specialist Capabilities
Air/inert (N2) drying gas
Applications
Early formulation screening and development
ProCepT 4M8-TriX Spray Dryer
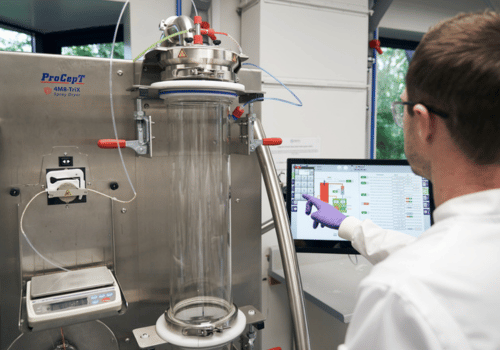
3 UNITS AVAILABLE
Typical Batch Scale
100mg – 400g
Specialist Capabilities
2-fluid and ultrasonic atomisation
Applications
Smaller scale GMP processes. Particle engineering for nasal and pulmonary delivery
GEA Niro SD Micro Spray Dryer
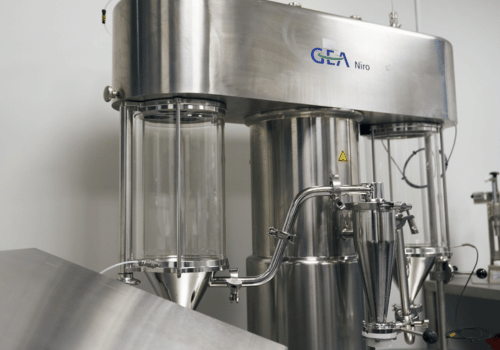
1 UNIT AVAILABLE
Typical Batch Scale
5g – 3kg
Specialist Capabilities
Air/inert (N2) drying gas
Applications
GMP manufacturing under nitrogen
GEA Niro MobileMinor Spray Dryer
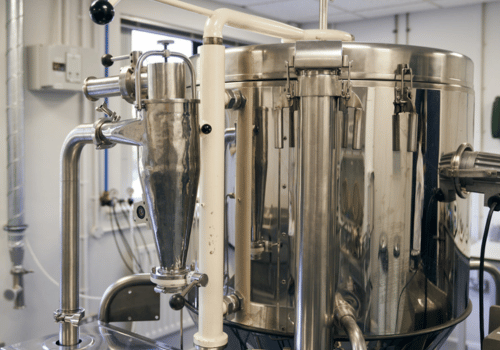
2 UNITS AVAILABLE
Typical Batch Scale
25g – 5kg
Specialist Capabilities
2-fluid and pressure nozzles
Applications
Larger scale aqueous spray drying
Key Considerations for SDD Development
Formulating SDDs requires selecting appropriate excipients like polymers and surfactants. Polymers such as PVP, HPMC, and Eudragit act as carriers to stabilize the API. Surfactants like SLS and Tween enhance wettability and prevent aggregation. Pre-formulation studies assess solubility, drug-polymer miscibility, and stability under storage conditions.
Process Optimisation
To achieve desired results, you must optimize spray drying parameters, including inlet temperature, droplet size, feed rate, and drying gas flow. These factors influence particle size, morphology, and stability. Consistent monitoring ensures efficient production and high-quality outcomes.
Quality & Stability
Maintaining the stability and consistency of SDDs is essential. Analytical techniques like microscopy, DSC, and XRPD help assess particle size, morphology, and amorphous content. Regular stability testing under controlled storage conditions ensures product reliability over time. Adhering to good manufacturing practices (GMP) minimizes process variability.
Scale-Up and Commerical Production
Scaling up requires selecting equipment with appropriate capacity and maintaining process efficiency. Parameters optimized at small scales may need adjustments during commercial production. Consistent product quality and regulatory compliance are critical during this phase.
Conclusion
Spray-Dried Dispersions address API solubility challenges by enhancing aqueous solubility and bioavailability through amorphous solid dispersions. Optimizing spray drying parameters and excipient selection ensures the stability and performance of SDDs. Adhering to quality standards and regulatory requirements supports the production of effective, consistent drug products.
Frequently Asked Questions
What Makes Spray Dried Dispersions Effective for Improving Solubility?
SDDs create an amorphous solid dispersion, increasing solubility in aqueous media. This leads to enhanced dissolution rates, ultimately achieving superior bioavailability compared to crystalline drug forms.
How Does the Choice of Excipients Impact the Performance of an SDD?
Excipients, particularly polymers, influence an SDD’s stability and dissolution. The right selection ensures proper matrix formation, stability, and controlled release, ultimately affecting the SDD’s effectiveness.
What are some common solubility issues encountered when formulating APIs?
Common solubility issues include poor aqueous solubility, slow dissolution rates, and low bioavailability, leading to challenges in achieving therapeutic drug levels and formulating effective products.
Are there any challenges or limitations associated with the use of spray dried dispersions for APIs?
While effective, spray drying requires specialized equipment and expertise. Potential challenges include selecting suitable excipients, optimizing process parameters, and managing production costs during development.
Can spray dried dispersions be customized for specific APIs based on their solubility profiles?
Yes, spray dried dispersions can be customized to address specific API solubility profiles by tailoring the choice of excipients, polymer ratios, and process parameters. This customization allows for targeted improvements in solubility, dissolution rates, and bioavailability based on the unique characteristics of each API.