What is Granulation?
Granulation has been widely used in the pharmaceutical industry since the 1950s. Whilst the science remains largely identical to that developed over 70 years ago, granulation techniques and equipment have improved to allow for a greater number of applications in both R&D and manufacture.
Granulation is a process where primary powder particles are blended and adhered to form larger, multiparticle entities called granules. Granulation is a crucial process in the pharmaceutical industry and is used to improve processability of solids, control dissolution profiles of a drug and eliminating poor content uniformity in final dosage forms. It’s often the first processing step when multiple formulation components are combined.
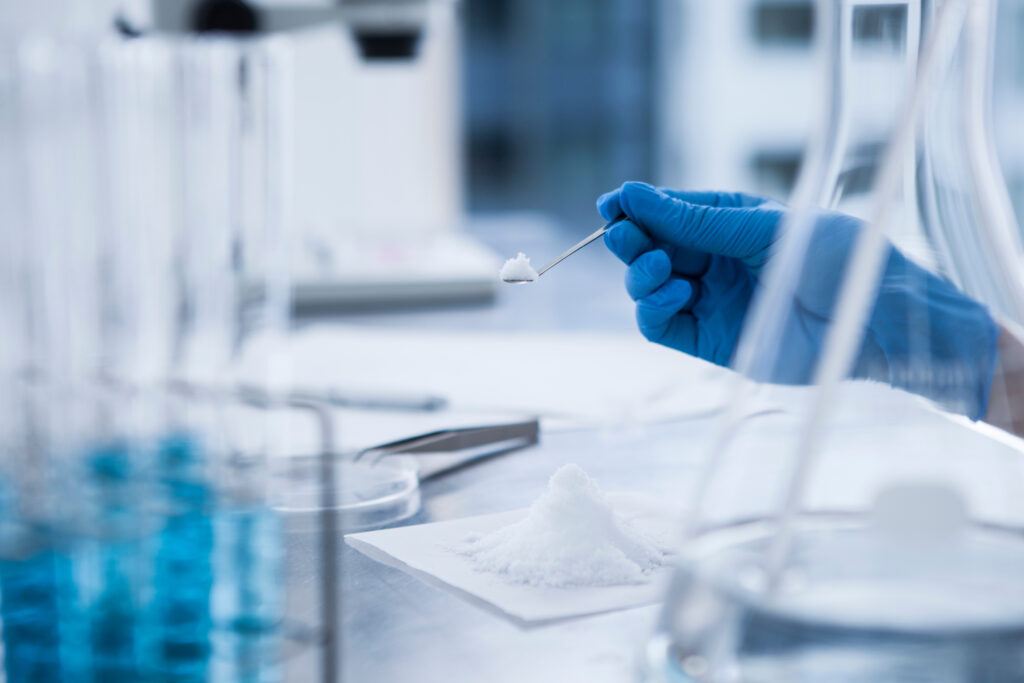
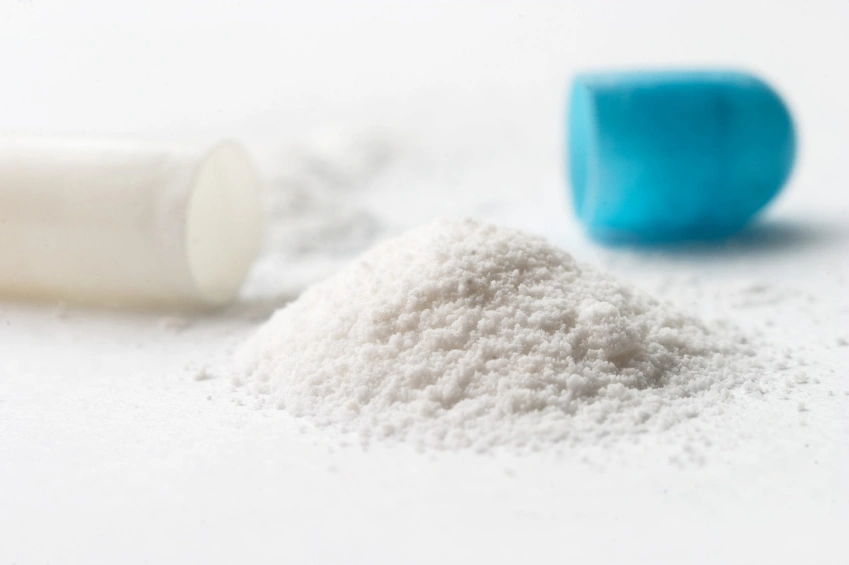
Pharmaceutical granulation is mostly used for tablet dosage forms, other applications include: capsules, sprinkle products for paediatric patients and production of engineered particles for modified release.
The reasons for granulating a pharmaceutical API can be any or several of the following:
- To increase the uniformity of drug distribution in the product
- To densify the material
- To produce “dust free” formulations
- Optimise dissolution profiles of tablets
- To enhance powder flow and powder handling
- To prevent powder segregation
- To improve the appearance of a final product
Discover Upperton's Oral Dosage Form Capabilities
Oral administration remains the most widely used route for the successful delivery of active pharmaceuticals to patients. Discover how a CDMO partnership can streamline your drug development journey.
Wet Granulation
Wet granulation techniques consist of homogeneously mixing the API with other powder excipients and wetting them in the presence of a binder or granulating fluid, forming larger agglomerates / granules. The wet granules are dried to remove moisture and then either screened or milled to eliminate oversized agglomerates and to control the particle size distribution.
Wet granulation is a complex process with a combination of several critical formulation and process variables greatly affecting the outcome. For example, determination of the granulation endpoint is still considered by many to be a fine art, requiring knowledge gained through years of hands-on experience. The window for liquid addition can be very narrow and over-wetting of powder can lead to the entire batch being completely unusable.
Wet Granulation Process
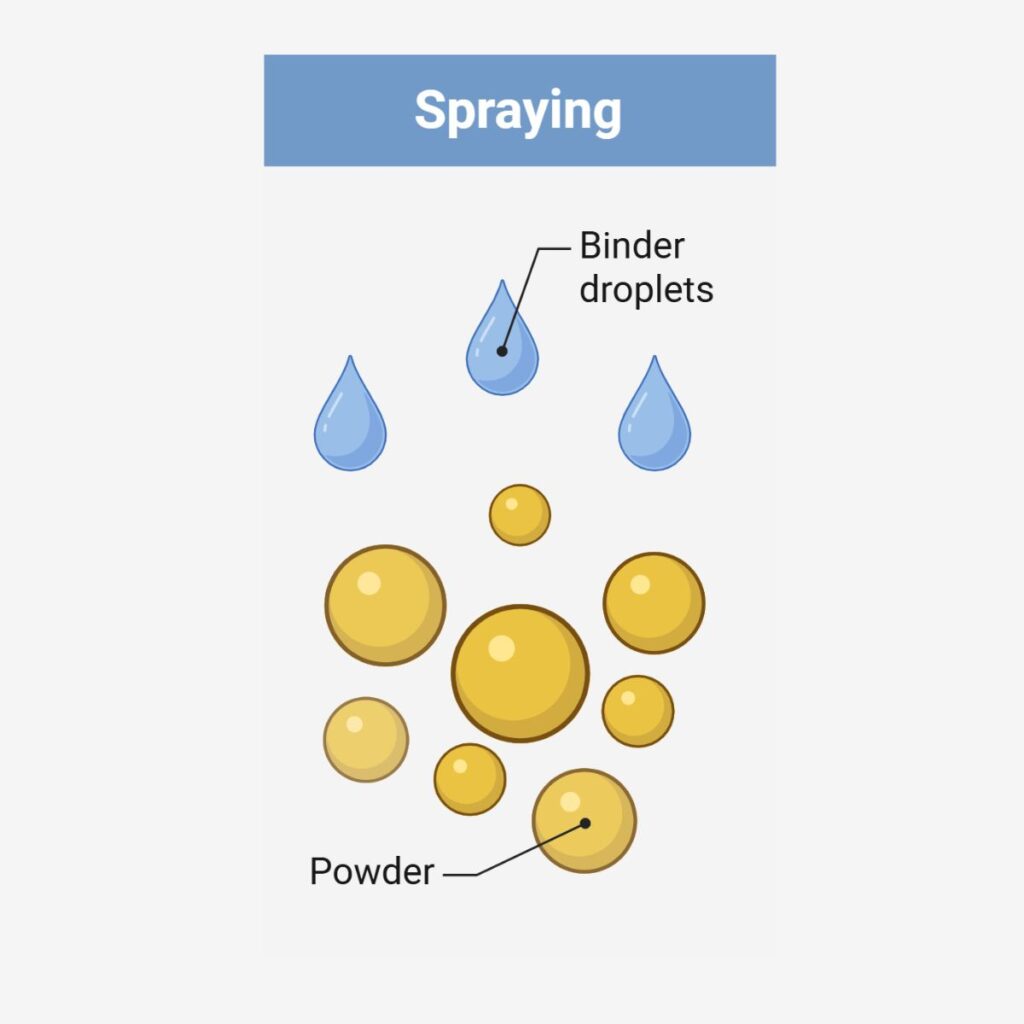
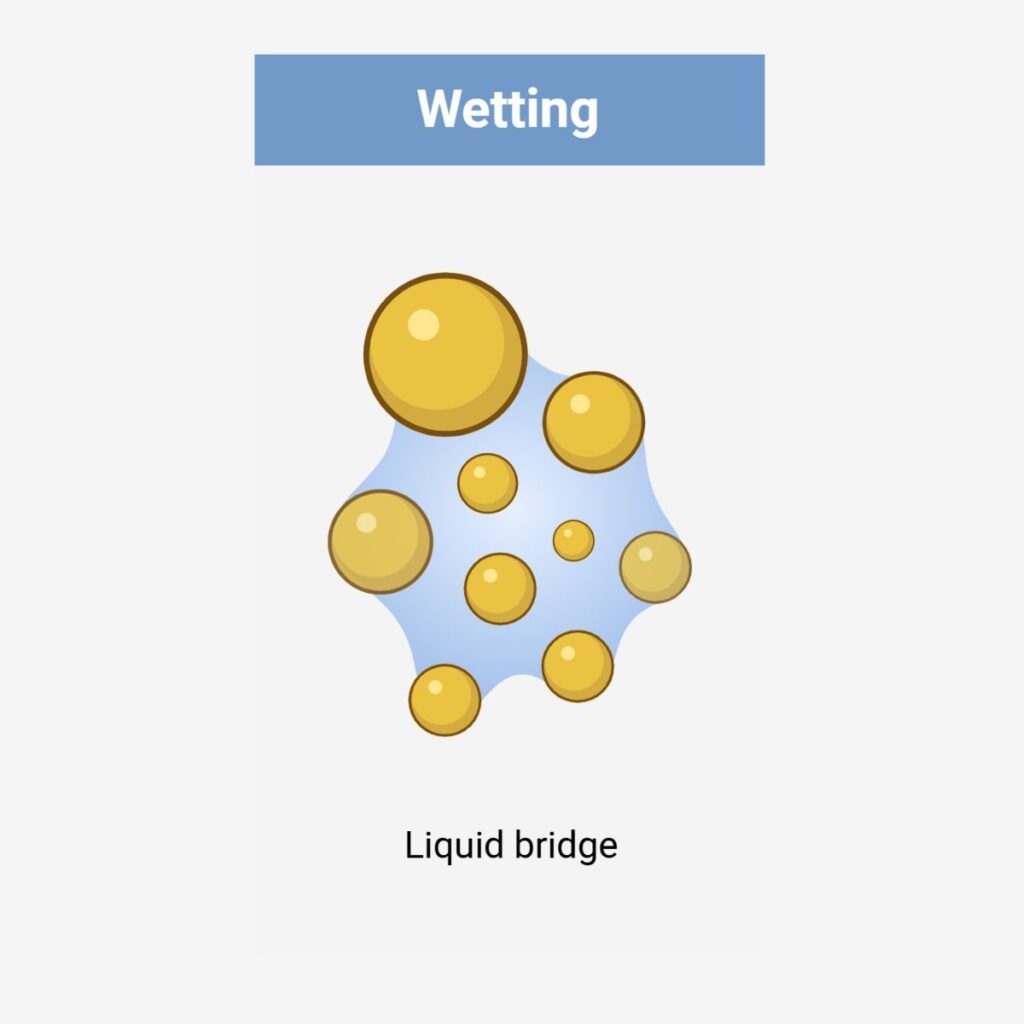
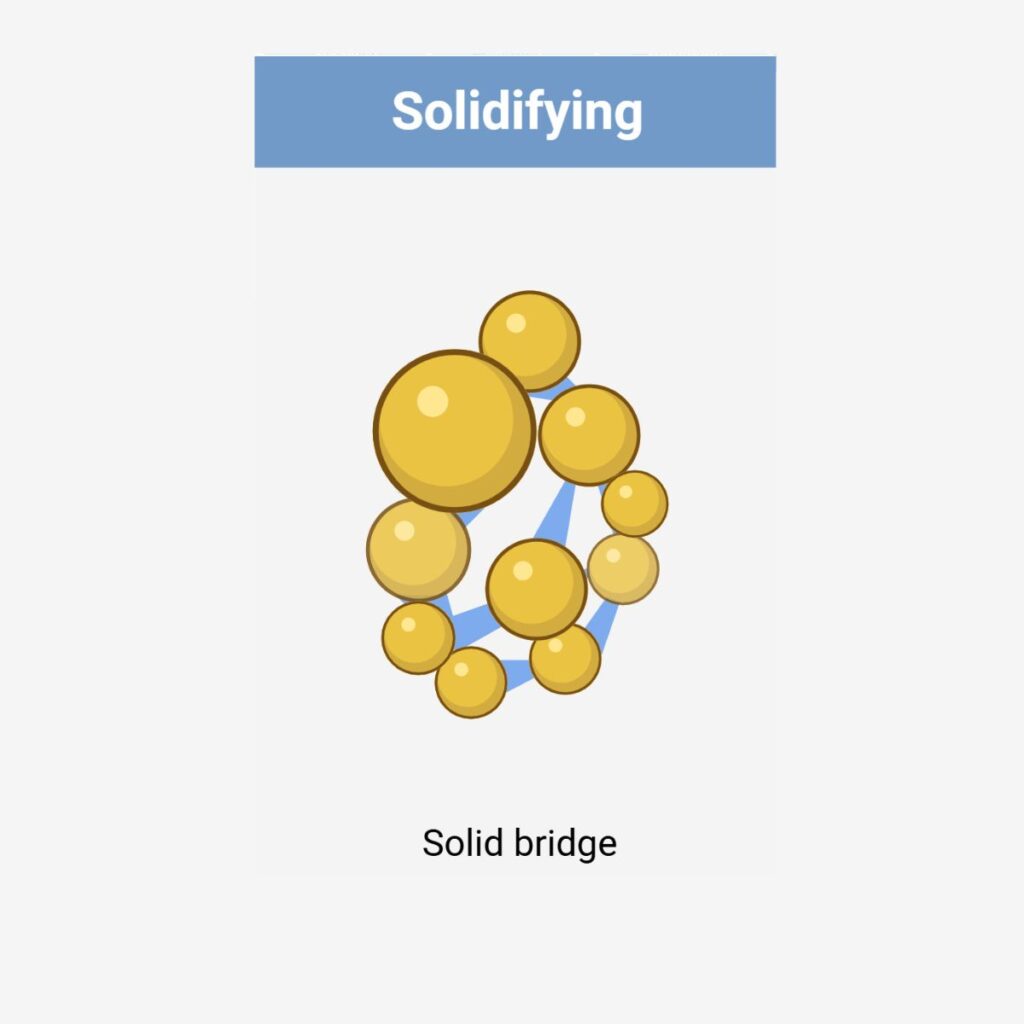
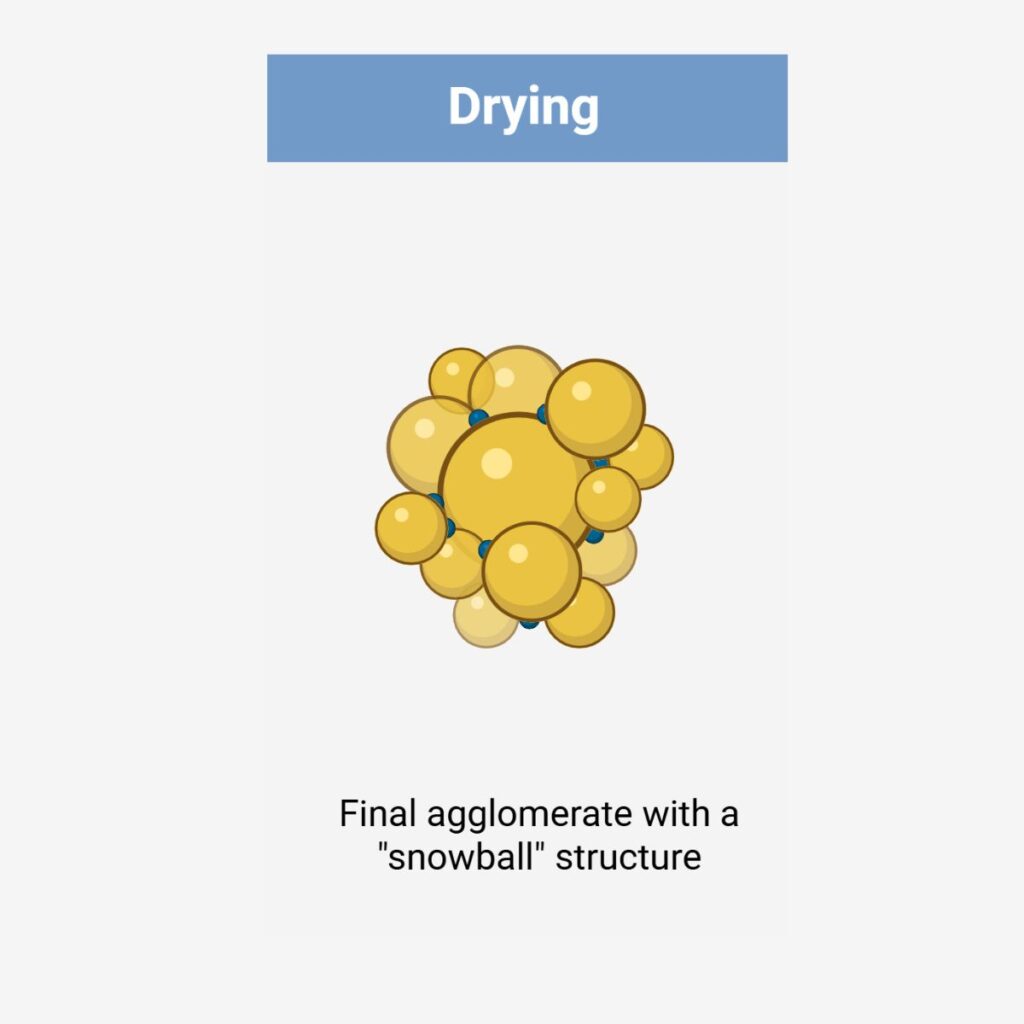
Wet Granulation Options
Wet granulation can be split into four main options:
Low-Shear Granulation
This is the traditional means of granulation. It employs low speed planetary or trough mixers, in which the drug and intragranular excipients are granulated with a binder solution.
The resulting wet mass is screened to form discrete granules and typically dried in a tray or fluid bed drier. Dried granules are re-screened / milled to the required size, blended with extra-granular excipients and lubricated. The main disadvantages of this process are the open nature of the equipment, the manual transfer of the materials being processed and the long drying times.
High Shear Granulation
High shear mixer granulators are characterised through the concurrent use of two mixing blades: an impeller that rotates in the base of the mixer and a high speed “chopper” that continually breaks up the wet mass as granulation proceeds. This combination provides a very effective mixing of components with lower amounts of granulation fluid compared to low shear granulation. The entire process of mixing and granulation can be completed in a few minutes. Systems can be fitted with a variety of devices to monitor and determine the end point of granulation. A high shear mixer granulator is a closed vessel and the granules produced are generally able to be transferred to a drier in a closed system, thus minimising the extent of handling. A key advantage of high shear granulation is its wide applicability to almost any formulation including high potent products.
Extrusion-spherisation
A uniform blend is required for the extrusion-spherisation process, which is wetted prior to manufacture. The process involves two manufacturing steps, extrusion through a circular die or multiple-die plate (often a screen) to generate rods or strings of material; followed by spheronisation where the extrudate is spun on a patterned plate, causing the rods to be fractured and become rounded into granules. The size distribution and surface characteristics of the spheres are controlled by batch size, speed, process time and the characteristics of the extruded mass. The main issue with extrusion-spherisation is that it is a multistep, labour intensive and time-consuming process.
Fluid Bed Granulation
Drug and excipients are loaded into a fluid bed processor, granulating fluid is sprayed into the bed with a continuous stream of warm drying air. These processes occur simultaneously producing a more streamline mixing, granulation and drying operation. However, it can be much harder to achieve high density material compared to the shear granulation methods; additionally, fluid bed driers can be expensive to acquire and to run due to the high volume of granulating liquid required.
The main disadvantage of both high and low shear granulating is that the granulation fluid (typically water) is intimately mixed with the formulation components. Water may be in contact with these components for a significant time, as a consequence water activated changes to drug and excipients may occur.
Advantages and Disadvantages of Wet Granulation
Advantages
- Improves the flow properties of materials
- Improves material compression and densification
- Easy to obtain a homogenous mixture – essential for low dose products / low drug loading
- Reduces in process air pollution due to liquid addition, preventing dust
- Reduces generation of static charge
Disadvantages
- Possible loss of material due to multi steps
- Initial installation can be expensive and require lot of space
- Complex process that can be difficult to control
- For moisture / heat sensitive materials it can cause instability
Dry Granulation
Dry granulation is a process whereby granules are formed without the aid of any liquid solution. The primary powder particles are aggregated at high pressure. The process can be used if the ingredients to be granulated are sensitive to moisture or heat.
Dry granulation is a two-step process: first a compression step to convert the powder into compacts, ribbons or flakes, then apply a milling step to break up these intermediate products. There are two main processes for the first step of dry granulation, slugging or roller compaction.
Dry Granulation Options
Slugging
In slugging, the dry powders are compacted with a conventional tablet machine or a heavy-duty rotary press. Slugs produced are then milled to create granules. This is traditional method has been largely phased out with the introduction of process specific roller compaction equipment. The main disadvantage of slugging is its poor reproducibility and control of the compacts produced. This variability can lead to poor flow rates and differing mechanical strengths of the slugs. Slugging can still be used successfully at an R&D level as a quick view into a formulation’s compressibility.
Roller Compaction
Roller compaction involves the powder mix being squeezed between two counter-rotating rollers. Roller speed and pressure can be adjusted and maintained during a run, meaning the sheets / flakes /ribbons produced are more consistent than the compacts produced during slugging. The sheets, flakes or ribbons are then milled to produce granules. Often a sieving process is required to remove any fines.
Roller compaction has the advantages of being a continuous process, having more defined and controllable processing parameters, being simpler to scale-up and producing product having uniform mechanical strength.
Advantages and Disadvantages of Dry Granulation
Advantages
- Elimination of exposure to moisture and therefore no need for drying step
- Less equipment, time and space required
- Removes cost / need of binder solution
- Improves the flow properties of materials
- Improves material compression and densification
- Mechanical strength of product is uniform
Disadvantages
- Dust formation in the environment and potential contamination
- High forces could be damaging to some active compounds
- Loss of available compressibility for tablet compression
- Requirement for double lubrication of product
Let's work together
How can we help you?
To Conclude
Pharmaceutical granulation techniques continue to be developed and improved with modified / novel technologies and processing equipment. Selecting the most appropriate technique continues to be based on a thorough understanding of the API’s physio-chemical properties and careful consideration of both processing properties and final product attributes. Upperton offers solid dosage form development using both wet and dry granulation techniques; using the Freund Vector TFC-LAB Micro Roll Compactor and GP1 High Shear mixer granulator. Upperton also has access to compaction simulation and large-scale roller compaction equipment.
Get in touch.
If you’re looking to work with a CDMO that can support your product from preclinical development to market and beyond, then we’re here to help.
Speak to our team to discuss your requirements.