- What we do
-
-
Routes of delivery
- Oral
- Nasal
- Nose to Brain
- Pulmonary
- Parenteral
-
Development stage
- Pre-clinical
- Phase I to Phase II
- Phase III - Commercial
Our Approach
- Selecting Your CDMO Partner
- Project Management
-
- About us
-
-
A CDMO like no other
- About Us
- Our Facilities
- Our History
- Awards and Achievements
-
Leadership Expertise
- Executive Leadership Team
- Board of Directors
- Careers
-
-
- Resources
- Events
- Contact
Scale-Up and Tech-Transfer.
Supporting you into the later stages of development
We understand the complexities of scale up and technical transfer. Covering all aspects from equipment consideration through to manufacturing handover and QC, our experience and capabilities ensure a seamless tech transfer enhancing product quality and reducing timescales.
Technology Transfer.
Our team of experts can support you in all aspects of scale-up and technology transfer through our state-of-the-art development and manufacturing facility.
With knowledge across all layers of our business, we ensure a seamless transfer and reduced risk of advancing into later stages.
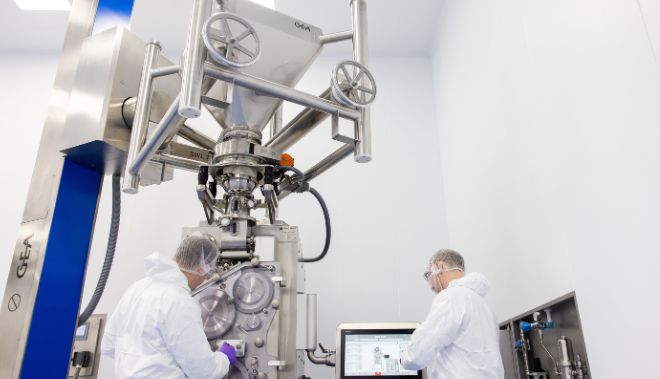
Scale-Up.
We support our customers at all stages of development and have a strong track record of scale up.
Our expert technical knowledge is supported by a unique project management approach supported by all layers of our business.
With Executive Leadership Team oversight on every project, you can have confidence in your drug program progression from grams to kilograms.
Our team applies the principles of quality by design (QbD) and a design of experiments (DoE) approach to development ensuring robust formulation and quality management.
sqft
0
MHRA Approved Research and Development, Analysis and GMP manufacturing facility.
sqft
0
warehouse with Schedule I-IV Home Office Approval.
tabletting capacity
0
Per day.
capsule filling capacity
0
From 500 per day up to 350,000 per day.
GMP suites
0
Individual state-of-the-art GMP suites with integrated QC and RD laboratories.
kg
0
Blending capacity from 500g to 250kg.
kg
0
Spray drying batch sizes from 0.5g to 10kg (aqueous and solvent).
units per day
0
Blister packaging capability.
Project delivery.
Our project teams are made up of subject experts from across our business, so you know you’re in good hands.
We provide an open dialogue to provide full transparency of project delivery, ensuring your scale-up and technical transfer requirements run smoothly.
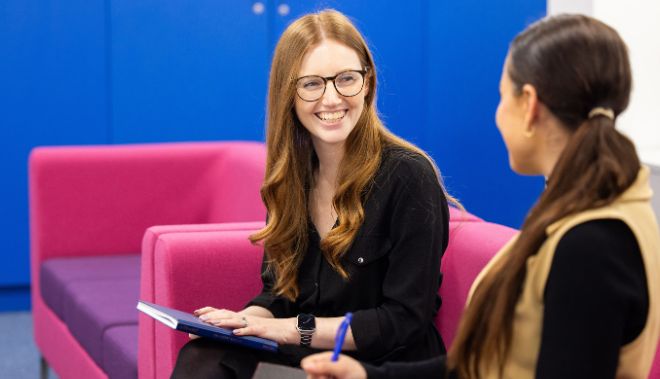
We're here to help
If you’re looking to work with a CDMO with extensive experience in technical transfer and scale-up, then we’re here to help.
Speak to our team to discuss your requirements.
Frequently Asked Questions
What are some common strategies used to optimize efficiency and productivity during process scale-up in pharmaceutical manufacturing?
During process scale-up, common strategies used to optimise efficiency and productivity include conducting thorough risk assessments to anticipate potential challenges, leveraging automation and advanced technology for accurate measurements and data analysis, optimizing equipment design for scalability, implementing continuous improvement practices, and ensuring clear communication and collaboration among cross-functional teams involved in the scale-up process.
What are the advantages of using spray drying in pharmaceutical formulations?
Spray drying offers several advantages in pharmaceutical formulations, including precise control over particle size and distribution, improved solubility of poorly soluble drugs, enhanced bioavailability, ease of scale-up, and versatility in producing various dosage forms such as powders, granules, and microspheres.
What types of pharmaceutical products can be produced using spray drying?
Pharmaceutical spray drying can be used to produce a wide range of products, including inhalable powders for pulmonary and nasal delivery, solid dispersion systems (SDDs) to improve drug solubility, modified release formulations for controlled drug release, and stable formulations of biologics.